Impossible, made possible. One layer at a time
1. Start with the best materials
We use grade 23 titanium - a better choice than the grades 2 and 5 titanium commonly used in watchmaking.
Grade 23 is tougher (more resistant to fracturing) and even friendlier to skin (‘biocompatibility’), thanks to its very low oxygen content (0.013%).
That’s why it’s commonly used by aerospace and biomedical companies. If it’s good enough for them…
2. Fire up the lasers!
Our process is called Laser Powder Bed Fusion (L-PBF).
This builds the watches using lasers to ‘sinter’ titanium powder - heating it to over 1,660°C, at high pressure, to form a solid shape.
It does this one layer at a time - each one is just 0.06mm thick - until the complex and unique case is complete.
If you’re an engineer (or just a massive geek) we use the latest Renishaw 500Q Flex machines. They’re good!
3. Prepare the case for heating
Because we use titanium powder, at this stage the cases are a bit…powdery. So the machine uses fine brushes to remove 99% of any powder that’s left behind.
We then shake things up, putting the cases in a high-frequency oscillating machine. This helps get rid of any final specks left inside the complex geometrical shapes.
4. Turn up the heat
Next up, we put the cases in a precisely controlled furnace, heating them at 850°C for two hours, a process called ‘annealing’.
Heat treatment helps make the cases stronger, relieving any residual stresses and making sure we’re making the most of the mechanical properties of the grade 23 titanium.
5. A sharp cut and finish
During the build process, the cases are welded to a ‘build plate’ - so they need to be removed.
We do this using Electrical Discharge Machining, a non-traditional type of precision engineering, using heat to cut the cases away, rather than mechanical force.
Once the cases are detached, we carry out the final ‘finishing’ - just enough to make them look sharp and feel good, but not so much that it removes the distinctive hallmarks of the additive manufacturing process.
.webp)
Impossible. Strong. Responsible.
Zoom in our cases and you could be mistaken for thinking you’re in an alien cityscape. The geometries look organic and beautiful - but unlike anything you’ve seen before on a watch.
This is all thanks to additive manufacturing (AM).AM means we build our watches one layer at a time, until we end up with the final, complete 3D design. This approach lets us build shapes and designs that were previously impossible - so our designers end up with the vision they saw in their heads, not a compromise.
AM also lets us create watches that are incredibly light but extremely strong. A complex mesh of fluid lines and impossible angles creates an immensely robust structure, not possible using traditional methods. It’s also inherently sustainable. As it ‘adds’ material, it’s almost waste-free.
This is the exact opposite to traditional ‘subtractive’ manufacturing used in the rest of the industry, which starts with a block of raw material and carves, cuts and chips away, discarding anything that isn’t needed.
Build British
Read more about who we work with across the country
Build British
Read more about who we work with across the country
Less, but better
We’ve built a watch that we hope will be with you for your lifetime - and maybe even passed on to the next generation. So we need to make sure that we play our part in making sure there’s a happy, healthy and habitable world for them to enjoy it in.
Our AM approach is inherently sustainable, creating minimal waste - especially compared to traditional watchmaking methods. We work with as many British suppliers as possible to build and assemble our watches - and choose them for their own sustainability creds - helping minimise our manufacturing emissions.
Because all the innovation in the world means nothing if it destroys our planet.
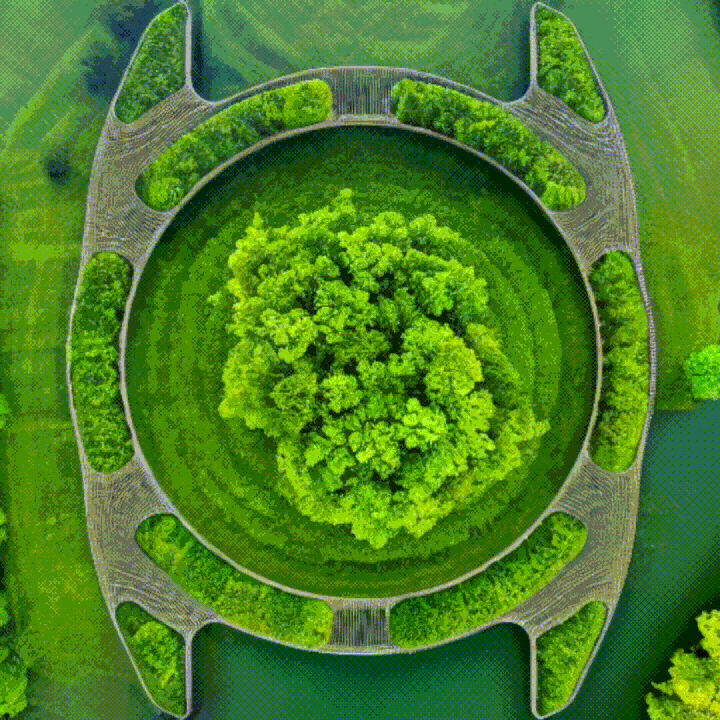
Join us on our mission
.png)
.png)
.png)